- PROTOTYPE MACHINING
- PRODUCTION
- SCORECARD
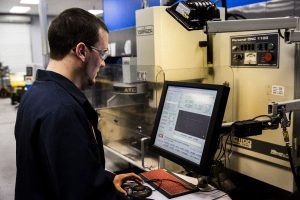
Fair-Rite continues to invest in state-of-the-art machining equipment to provide you with quick-turn prototypes for proof of concept prior to production tooling commitment. This allows our customers to quickly evaluate their design, experiment with different materials and geometries, and determine the final product while maintaining their development schedule and budget. What differentiates Fair-Rite is the expertise we provide our customers to help optimize their design to go from quick-turn prototypes to an economical, press-to-size part.
In a world of continuous innovation, rapid prototyping is essential. Machining ferrite parts reduces lead-times from months to weeks and is significantly more cost-effective than fabricating tooling when designs are changing between prototype runs. The ability to machine parts on small-scale production is useful for those with evolving designs. For those type designs that cannot be a press to size part, that must be maintained as a machined part, Fair-Rite has the capability to support volume production machining. Engineering assistance is available to guide you through the prototyping process to ensure the best performance in your application. This is the essence of our Design, Develop, Deliver strategy!
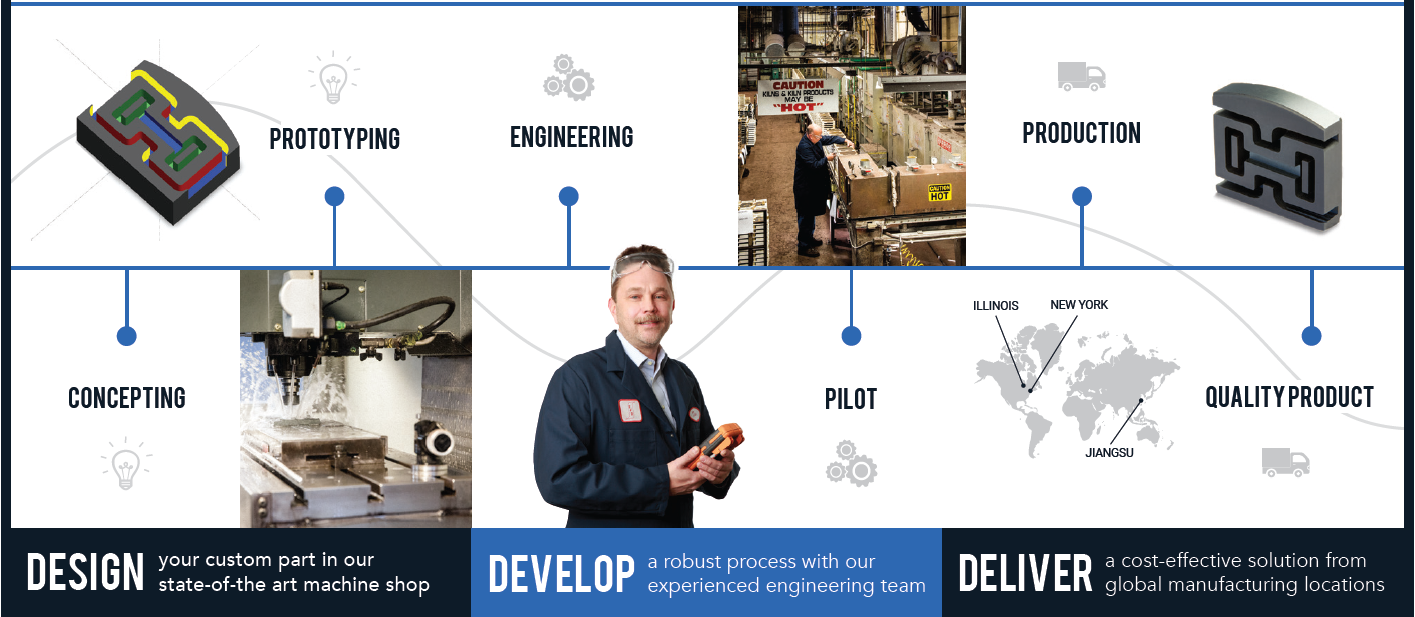
Being a ferrite manufacturer, Fair-Rite ensures the quality of our material before it reaches prototyping – meaning fewer defects and a superior end-result. With our extensive experience with ferrite manufacturing, we are able to help move from small runs to large scale production seamlessly. Our engineers will provide input to design for manufacturability, ensuring the most cost-effective processes are used while still maintaining design integrity.
Once the design is finalized, Fair-Rite will work with you to determine appropriate mechanical and electrical specifications to ensure meaningful testing for the customer’s application.
Capabilities Include:
- CNC machining
Fair-Rite’s Prototype Machining - Gapping
- Drilling
- Slicing
- Milling
- Surface Grinding
- Profile Grinding
- ID Grinding
- OD Grinding
- Lapping
- Slotting
- Cutting
Example Geometries:
- Connector plates
- Rotary transformers
- Suppression plates
- Pot-cores, E-cores, and other power parts
As we continue to be ‘Your Signal Solution’, let us help make your designs a reality with our State-of-the-Art Machine shop!
For more information about our machining capabilities, please contact our Business Development Manager, Jerry Barbaro at barbaroj@fair-rite.com or (845) 895-2055 extension 603.
Powder Preparation
Fair-Rite has the capability to produce and test our own powder to ensure high-quality products starting from the very beginning of the process – the raw material. We implement in-process controls such XRF and pre-production powder lot evaluation to ensure the proper composition is maintained. Fair-Rite has tight composition control and each lot of powder is verified to control physical and electrical characteristics before it is released to production.Forming
Dry Pressing
The method of dry pressing is the most common way to form ferromagnetic powder into meaningful shapes. To do this, the powder must be mixed with binder and lubricants before being compacted. A press tool set typically consists of an upper and lower punch held within a die. The movement of these punches, along with the die, is done in a specific sequence such that the density of the formed part is uniform. Uniform density is important to ensure consistent electrical and physical properties throughout the part. The size of the press required, meaning the amount of tonnage required for a particular part, is dependent on the size of the part. This process compacts powder only along one axis. Therefore, parts having details not along the axis of compaction cannot be manufactured solely utilizing the dry pressing process – instead, additional machining steps would be necessary or a different forming process is needed. Tool design is a critical aspect of dry pressing. At Fair-Rite, this design is performed by our in-house experts who have extensive experience. As part of the process, we will work with our customer to utilize our expertise and develop a tooled solution to meet your specification. At Fair-Rite, we have the capabilities to produce components 250 cm2 by 18mm thick and 34 cm2 by 80 mm long. Call for custom capabilities to meet your design needs.Injection Molding
For relatively small parts with more intricate features that cannot be generated with traditional dry-compacting process, injection molding is used. In this process, the plasticized material is forced in to a mold to achieve the desired shape. These are for designs that have features not along the axis of compaction in dry-pressing.Sintering
Material | Firing |
Nickel Zinc (NiZn) | Air |
Manganese Zinc (MnZn) | Atmosphere |
Manganese (Mn) | Atmosphere |
Magnesium Zinc (MgZn) | Air |
Finishing
Burnishing
Depending on the part, some 'flashing' may occur at its edges making them sharp. In order to remove the 'flashing', these parts are tumbled in large bowls with media. Removing the sharp edge (flash) reduces the possibility of damaging wire insulation in the end application.Grinding
Centerless Grinding
Fair-Rite is exceptional at processing cylindrical parts that require tolerances of 0.025mm or tighter on their outside diameter using our centerless grinding process. We are currently capable of cylinders between 0.5mm and 30mm in diameter, and up to 75 mm in length.Plunge Grinding
In some cases, features within a part cannot be achieved in the “forming” stage and thus requires some post-processing. To this point, plunge grinding is used to create a bobbin from a rod reliably and cost-effectively. Call us to discuss your specific requirements.Surface Finishing
For either mechanical or electrical purposes, some parts require a certain flatness specification to function properly. To achieve this, Fair-Rite has the capability to grind the surface of these parts using various methods; depending on the process an average surface roughness is 0.85 µm and can be as smooth as 0.25 µm through feed, polish and lapping.Gapping
Generally done for power parts, gapping is a process of introducing an air-gap in a part in order to increase its ability to handle electric current. Fair-Rite offers standard sizes of products for your power applications and can hold some AL values of +/- 2% and mechanical gaps as close as +/- 0.001”.Annealing
Through the annealing of certain materials, Fair-Rite has the flexibility to change the electrical properties of the parts to meet certain requirements. Please contact us for more information.Coating
Parylene coating
Fair-Rite offers Parylene coating for select parts. This colorless conformal coating is used on smaller parts due to its higher cost but minimal coating thickness. Fair-Rite currently uses Paralyne-C material:Property | Value |
Dielectric Strength | 5600 V/mil |
Volume Resistivity | 8.8 x 1016 ohm-cm |
Surface Resistivity | 1014 ohm |
Dielectric Constant (1 MHz) | 2.95 |
Dissipation Factor (1 MHz) | 0.013 |
Density | 1.29 g/cm3 |
Water Absorption (24 hours) | < 0.1% |
Coefficient of Friction | 0.29 |
Continuous Operating Temperature | <100°C |
Thermal Conductivity | 2.0 x 10-4 cal/sec/cm/°C |
Maximum Operating Temperature | <160°C |
Thermo Set Plastic coating
Fair-Rite also offers the ability to coat parts with epoxy. Due to the minimum coating thickness of 0.005”, this method is reserved for parts that are larger in size (diameters > 9mm).Quality
Vision System
For parts that require 100% optical inspection, Fair-Rite has developed its own automated vision system to ensure all parts are within mechanical tolerances and there are no unacceptable chips, cracks, or voids. This is specific to rods and shield beads, and Fair-Rite currently processes parts from 0.5mm to 5mm in OD and 5mm to 15mm in length.Toroid sorting
Toroids can be 100% sorted for inductance with our high-speed sorting equipment. These are typically used for higher perm parts when a tighter-tolerance is required.Capabilities

PROTOTYPE MACHINING

PRODUCTION
New York, Illinois and China – meaning you can expect the same quality from anywhere! Customers working with our engineers in the US to prove out their design can feel confident transferring their design for state-side or overseas production.
